Restoration: The many advantages of lime
An old building material, the many advantages of lime mean it can also be used on more modern stone houses as well
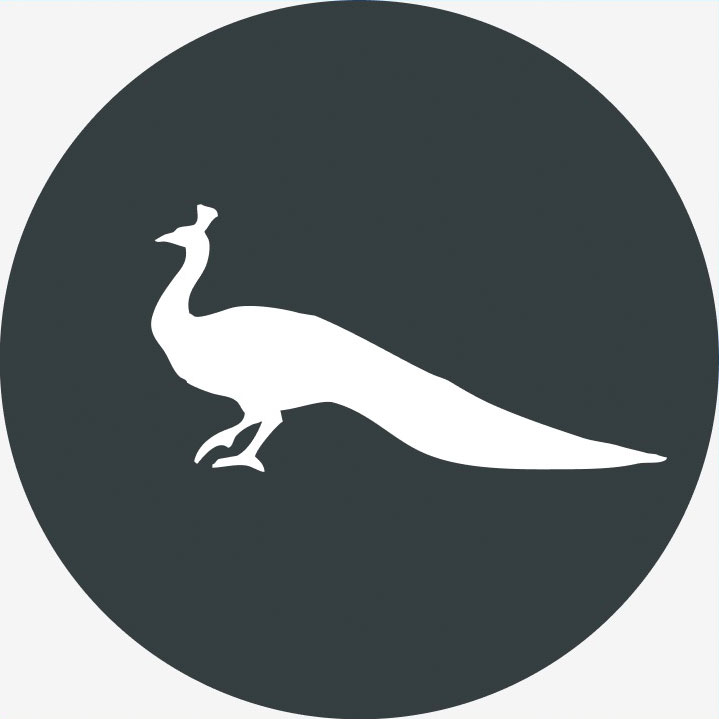
The answer is lime - what's the question? This is not as flippant as it sounds. Lime is the perfect building material. It's carbon neutral, recyclable, aesthetically pleasing and much, much better for buildings than its most commonly used alternative, cement - even in modern construction. Using lime can only help the long-term health of a building.
So why isn't lime used more often? Probably because it's more expensive and requires a level of understanding of its capabilities that isn't as common as it used to be. However, many in the construction industry are now rediscovering the virtues of this natural material. The Romans introduced the technology of lime to Britain over 2000 years ago, but it was used across the ancient world for thousands of years before that. Before cement was invented in the mid 19th century, most houses were built using lime mortars and plasters, but during a time of rapid construction in the early 20th century, cement was cheaper to buy and set more quickly, allowing buildings to be constructed faster.
In the early days of building restoration and preservation, cement was often used but it didn't take long to discover how damaging this was. Cement is dense and fragile, and when it's used to repair an old building it won't allow the passage of moisture, resulting in cracks. There is now a significant legacy of damage caused by inappropriate use of cement in old buildings by previous generations. However, the use of lime shouldn't be confined to the repair of old buildings. Heritage architects now recommend lime in the building of new houses too because of its qualities. It takes longer to set and needs specialist lime plasterers, but it improves the life and appearance of a building. No expansion joints are needed and it's self-repairing to a degree - when cracks appear, tiny granules of lime will trickle down to lodge themselves in the cracks below.
* Give Country Life for Christmas and save up to 40%
Whether a stone house is old or new, there's no point applying modern paint on top of lime mortar or plaster. It's like wrapping a building up in cling film - moisture has nowhere to go and will build up in the limestone causing damp problems and damage to the stones or bricks adjacent to the cement mortar joints. There are many ‘breathable' paints available, as well as traditional limewash or distemper with their subtle colours and beautiful finish.
Lime is produced by heating limestone, chalk or shell (calcium carbonate) to a temperature above 900 degrees centigrade. Carbon dioxide is given off and the material becomes calcium oxide (quicklime). Lime is created by adding water, known as slaking. If it contains impurities (such as aluminium or magnesium silicates), hydraulic lime is produced.
There are two main types of lime: Hydraulic and non hydraulic. Additives present in hydraulic lime (whether naturally occurring or subsequently added) will strengthen the mortar. Non-hydraulic is pure slaked lime. Modern hydraulic limes are increasingly being used in the repair of old buildings as they help strengthen a building while maintaining its porosity and flexibility. A good supplier, will be able to analyse a sample from an existing wall and produce a suitable match for repair.
Sign up for the Country Life Newsletter
Exquisite houses, the beauty of Nature, and how to get the most from your life, straight to your inbox.
Lime mortar is lime mixed with aggregates such as sand and animal hair (horse or goat for example), to strengthen and bind it. Lime plaster will also have animal hair added, though no aggregate. The beauty of lime is that as it sets, it re-absorbs the carbon dioxide as it returns to its original state of calcium carbonate (limestone), making it the perfect material for our time. For me, there is no question about it: For 21st century building and restoration, the answer is lime.
Neil Quinn is a Conservation Architect and Partner at Yiangou Architects, which was established in the Cotswolds in 1981. From its base in the historic town of Cirencester, the practice specialises in high quality residential construction using both traditional and contemporary materials. The practice's team of seven qualified architects is equally at home working with Grade I Listed or contemporary buildings, supported by a well-qualified and experienced team of technicians and technical co-ordinators. In recent years the practice has expanded and projects now extend nationwide. The company can also manage new projects from design through to building completion.
This is an article from ProjectBook which provides a wide range of information for the conservation, restoration, care and repair of period and listed buildings. Yiangou Architects are members of the Heritage Register which contains over 500 vetted craftsmen, contractors and consultants from all over the UK. Updated daily with new content, the website features the heritage register, a products directory, informative articles, current news, events and more. For more information, visit www.projectbook.co.uk.
Country Life is unlike any other magazine: the only glossy weekly on the newsstand and the only magazine that has been guest-edited by HRH The King not once, but twice. It is a celebration of modern rural life and all its diverse joys and pleasures — that was first published in Queen Victoria's Diamond Jubilee year. Our eclectic mixture of witty and informative content — from the most up-to-date property news and commentary and a coveted glimpse inside some of the UK's best houses and gardens, to gardening, the arts and interior design, written by experts in their field — still cannot be found in print or online, anywhere else.
-
Some of the finest landscapes in the North of England with a 12-bedroom home attached
Upper House in Derbyshire shows why the Kinder landscape was worth fighting for.
By James Fisher Published
-
John Sutcliffe — The man, the myth and the paint-naming legend behind Dead Salmon and Elephant's Breath
By Carla Passino Published