Doing up your dream house: Brick Maker
Mr Minter's knowledge of traditional brick making spans over three centuries.
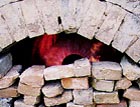
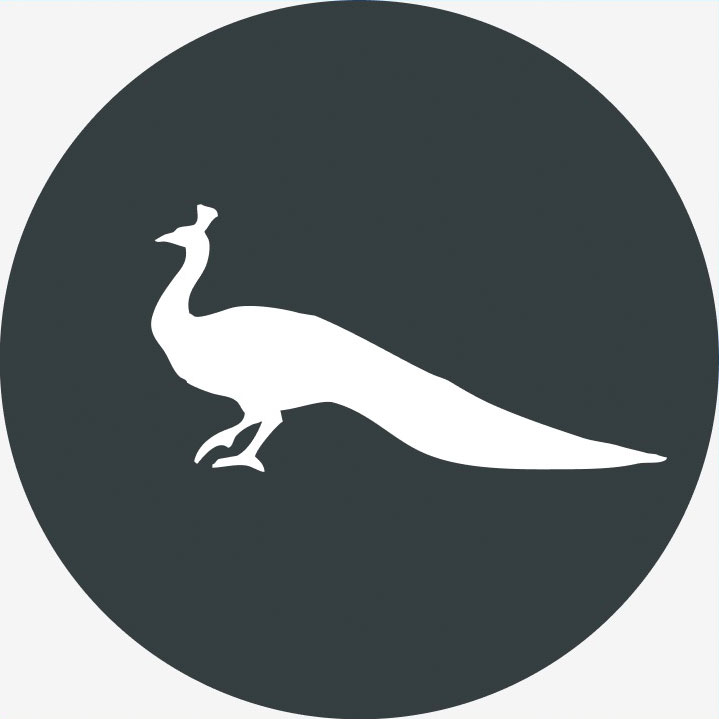
With their natural variations of colour and texture and irregularities of shape, handmade bricks possess a life and character that is not found in standard, modern brickwork. The clays from which they are made weather naturally, so that buildings constructed of them age beautifully, and sit well in the landscape. Handmade bricks have practical advantages, too, particularly when it comes to replicating traditional bonding patterns. Standard sized modern bricks, as used in the bland, stretcher bond brickwork that has become the norm today, are unsuitable for Flemish and English bonds. Until the Industrial Revolution, when bricks started to be mass produced and widely transported by canal, the use of brick was more regionally defined, and East Anglia, because of its lack of natural building stone, was one of the main brick-producing areas. Peter Minter's family firm, the Bulmer Brick & Tile Company, occupies a site on which brick kilns have been operating more or less continuously since 1450. His father bought the business in 1936, and today Mr Minter (aged 74) runs it with his two sons. Mr Minter's knowledge of traditional brick making is unrivalled. Indeed, his first hand experience spans three centuries, as he learnt all the tricks of the trade from men born in the 1860s and 1870s, who were too old to be called up in 1939. 'It was a time when most similar brickyards had to close down,' he says, 'but my father had built a new type of down-draft kiln, which could be blacked out during air raids. Because of this, and the fact that we had the right clay for making land-drainage pipes for fields and aerodromes, we were able to continue operating.' The end of the war heralded a mini boom, but this was soon followed by a crash, when nobody wanted handmade bricks anymore. Mr Minter's father, a builder by training, turned to restoring old cottages instead, for which he made his own non-standard-sized bricks, which were soon in demand from early restoration enthusiasts. When he died in 1974, Mr Minter dropped the building side of the business and concentrated on the brickyard. 'I was being encouraged to keep going because there was such a dearth of traditional skills and knowledge,' he says. Since then, the company has expanded to service mainly the conservation industry, making bricks to order in 100 different sizes, as well as 'specials' (bricks of non-standard shapes), some clay tiles, and 'rubbers'. The latter are made from specially prepared clay, which has been washed to remove all impurities. They are fired in blocks, and then cut to make voussoirs for arches and other decorative shapes. The company has been involved with numerous historic buildings, such as Hampton Court and St Pancras Station, which is currently having all its arches repaired. The brickyard lies on a seam of London bed Eocene clay and has two kilns, including a replica of Mr Minter's father's down draft model, built using his original drawings. Once the clay has been dug up, it is left out to weather over the winter. Then it is prepared, a process not unlike bread making. It is put through a mixing machine called a pugmill, from which it is fed onto the brickmaker's bench. A handful is then rolled into a warp, and thrown into a sanded mould. Any surplus is struck off, and the brick turned out onto a board. The 'green' (or unfired) bricks are then wheeled away on a special barrow to be dried. During the main brick-making season March to October they are left outside under shelters to dry, which takes about three weeks; in winter, they are dried in sheds. Then the firing process begins. 'It takes about two and a half days to load a kiln with about 12,000 bricks,' says Mr Minter. 'The kiln is heated by coal to between 1,000×C and 1,150×C, with the bricks nearer the top (where it is hottest) coming out darker. They spend three to four days in the kiln and are then left to cool for three days; it takes a further two days to unload them. We aim to fire the kiln about every two weeks.' MARY MIERS Bulmer Brick & Tile Co: 01787 269232 Top Tips
- Early planning is essential. Make your order well before you put up your scaffolding
- Don't be put off by imperfections found on old and handmade bricks, they are a natural feature, and part of their appeal
- Use lime mortar for pointing bricks, as cement mortars damage brickwork
Sign up for the Country Life Newsletter
Exquisite houses, the beauty of Nature, and how to get the most from your life, straight to your inbox.
Country Life is unlike any other magazine: the only glossy weekly on the newsstand and the only magazine that has been guest-edited by HRH The King not once, but twice. It is a celebration of modern rural life and all its diverse joys and pleasures — that was first published in Queen Victoria's Diamond Jubilee year. Our eclectic mixture of witty and informative content — from the most up-to-date property news and commentary and a coveted glimpse inside some of the UK's best houses and gardens, to gardening, the arts and interior design, written by experts in their field — still cannot be found in print or online, anywhere else.
-
About time: The fastest and slowest moving housing markets revealed
New research by Zoopla has shown where it's easy to sell and where it will take quite a while to find a buyer.
By Annabel Dixon Published
-
Betty is the first dog to scale all of Scotland’s hundreds of mountains and hills
Fewer than 100 people have ever completed Betty's ‘full house’ of Scottish summits — and she was fuelled by more than 800 hard boiled eggs.
By Annunciata Elwes Published
-
How to prepare your house for winter
As winter approaches, experts advise that preventative measures are crucial for our houses to weather hard winters
By Country Life Published
-
Ten house tips for the winter
Now is the time to put your house in ship-shape for the winter months ahead. Chartered surveyor Tom Grillo shares his ten top tips
By Country Life Published
-
Choosing an interior designer
Finding the right skilled interior designer for your period property requires some dedication; in particular you need to make sure you share the same vision
By Country Life Published
-
Maintenance tips for Victorian houses
There are a number of aspects to look out for when viewing or indeed owning a Victorian house
By Country Life Published
-
Best cooking pans
Mrs Danvers suggests the best makes of pots and cooking pans to hunt down when shopping for a special friend's wedding present
By Country Life Published
-
How to save old floorboards
Lots of care and elbow grease can help old floorboards gleam again
By Country Life Published
-
Buying bellows
Mrs Danvers recommends where to find a new or antique pair of bellows
By Country Life Published
-
Removing chocolate stains
Mrs Danvers tackles readers' household queries: this week's are chocolate stains on a linen suit and screen doors
By Country Life Published