Doing up your dream house: Architectural Potter
Mary Miers talks to an architectural potter who says we should accept no imitations when it comes to this very idiosyncratic skill
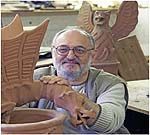
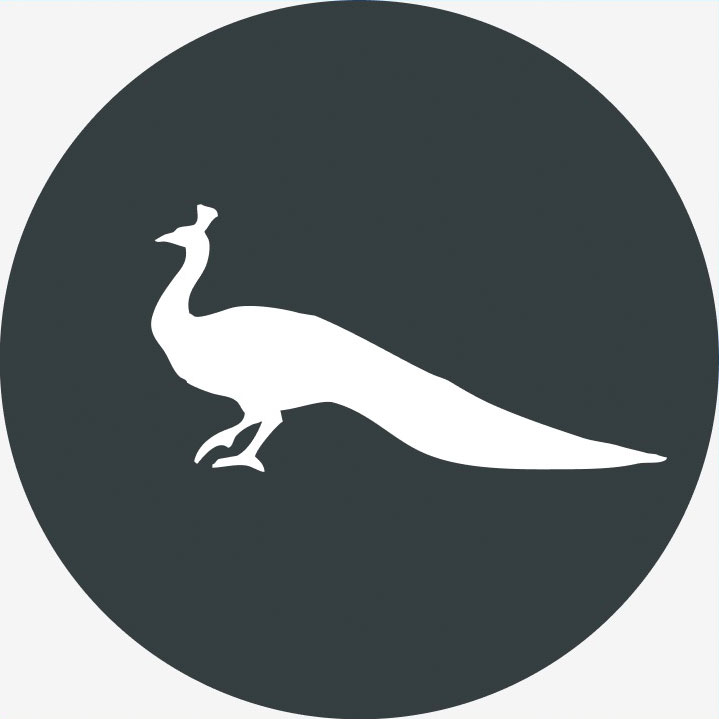
Architectural terracotta encompasses a wide range of ceramics, among which are the inventive details that embellish the skylines and façades of buildings, sometimes in a functional role. The potter Marek Drzazga-Donaldson hand-models a delightful array of architectural ornaments, replacing missing pieces, as well as making flamboyant new ones. The term terracotta, Italian for baked earth, generally refers to an unglazed fired clay, the refined particles of which give it a dense, impervious surface that weathers well and is suitable for semi-structural ceramics (the glazed counterpart being faience). The proportions of silica, alumina and iron oxide are crucial, the latter dictating the vivid reddish colouring typical of terracotta (although it can also be produced in buff and cream). Widely known since ancient times from Greece and Africa to China, the use of terracotta in this country reached its zenith in the late 19th century, when the Victorians animated the surfaces of buildings such as the Albert Hall with a riot of decoration, inspired by fine examples of Tudor work and Renaissance terracotta in Italy. Marek was brought up in Cookham, Berkshire, which he describes as 'full of dragons, decorative ridge-tile finials and a variety of chimneypots that amazed me as a youngster. As soon as I touched clay in my twenties, I knew I wanted to work with it'. After studying at art college in Maidenhead, he worked with the college's chief potter and taught there. He sold mostly domestic pottery until he embarked on larger architectural ceramics with a 43ft-long mural for Cookham's Institute of Marketing. He started making reproduction chimneypots and finials in 1988, and in 1995, moved to Devon, where he runs his present studio with his wife, Pauline. Marek rarely uses the traditional press-moulded methods of making decorative facings. Instead, he exploits the natural properties of clay for sculptural and decorative modelling. Working to commission, he creates birds, gargoyles and fantastical winged dragons. His repertoire includes ornamental chimneypots?perhaps barley-sugar-twisted or castellated? unusual roof fittings, inscribed plaques, and a range of ridge tiles?such as those on Philip Webb's Red House. His pieces sell widely abroad, dragons, costing from £450, being the most popular. Frost-proof clays from Valentines in Stoke-on-Trent are used, blended to produce the colour and characteristics of a particular locality. 'With my wheel, I throw the clay, modelling the parts and joining them together. The piece stiffens up naturally for a week before going into a drier for 4?5 days. It is then fired in a kiln for 3?4 days. If it's very large, I make individual parts and fix them together using epoxy resins and coloured sands.' Marek is dismissive of the factory-made, slipcast copies of his work, which he describes as 'untouched by human hand and horribly ugly. They lack the individuality of handmade pottery, the varying shapes, and the painterly effects of different firings'. Marek Drzazga-Donaldson, No9 Studio UK?01769 540471; www.no9uk.com.
Sign up for the Country Life Newsletter
Exquisite houses, the beauty of Nature, and how to get the most from your life, straight to your inbox.
Country Life is unlike any other magazine: the only glossy weekly on the newsstand and the only magazine that has been guest-edited by HRH The King not once, but twice. It is a celebration of modern rural life and all its diverse joys and pleasures — that was first published in Queen Victoria's Diamond Jubilee year. Our eclectic mixture of witty and informative content — from the most up-to-date property news and commentary and a coveted glimpse inside some of the UK's best houses and gardens, to gardening, the arts and interior design, written by experts in their field — still cannot be found in print or online, anywhere else.
-
A well-connected rural playground with 23 acres on the edge of the South Downs National Park
Old House Farm is an impressive family home with a wealth of amenities that would inspire any rural passion.
By Arabella Youens Published
-
The UK gets its first ‘European stork village’ — and it's in West Sussex
Although the mortality rate among white storks can be up to 90%, the future looks rosy for breeding pairs in southern England.
By Rosie Paterson Published