Doing up your Dream House: Antique carpet restorer
Avoid the effects of amateur botch jobs on carpets and rugs by having them professionally restored.
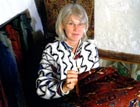
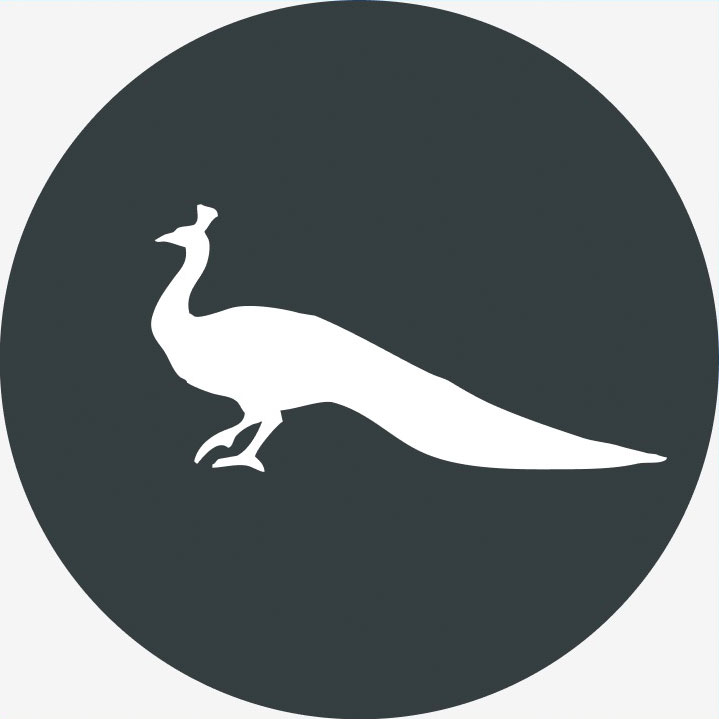
No item of a house's furnishings is subjected to greater wear and tear than its rugs and carpets. Some owners, in a bid to save money, attempt to carry out their own repairs using inappropriate yarns and even felt-tip pens to re-colour worn areas. Some address the problem of holes developing in valuable old rugs and carpets by cutting off the offending areas with scissors. Yet for a reasonable price £50, say, for the careful surface cleaning of a small rug; between £150 and £250 to have the sides and ends of a 6ft by 4ft rug repaired they could avoid the ill effects of amateur botching, and seek the advice and services of an antique-carpet restorer such as Jill Patchett. She and Alan du Monceau run a workshop in the 14th-century hall chamber of the Priest's House at Muchelney, their home on the Somerset Levels, which they rent from the National Trust. Here, working entirely by hand, they repair and clean Oriental and European rugs and carpets, as well as some textiles and silks, tapestries, suzanis and ikats. Most artefacts, such as the 30 rugs and carpets they have been working on from Batsford Park, are brought to them in the studio. However, if a carpet is too large or fragile to move, they will repair it in situ, as they did with a Robert Adam carpet that needed its rotted jute weft completely rewoven; it took them two years to restore. Alan concentrates on the fine needlework and technical side of things, and Jill's area of expertise is choosing and dyeing the yarns, and knotting the patterns. Having trained as an artist, she researched natural dyes and handspun wools in the early 1970s, and, a decade later, went to work in the conservation workshop of an antique-carpet business run by Alan in Cirencester. 'We use cotton, linen and, mostly, wool nothing synthetic,' she says, explaining how she chooses yarns not only for their texture and thickness, but also for their lustre. 'Over time, a carpet's wool becomes more lustrous than it was when woven. We must, therefore, source yarns that replicate this quality the wools we use come from a mill in Yorkshire.' Jill then dyes the wool (which arrives colourless), using a combination of natural and synthetic pigments. This process involves a lot of experimentation 'dyeing little bits different shades, comparing them to the rug in different lights; it's like painting a picture'. The colours would, of course, have been much brighter when the carpet was new it is Jill's job to replicate their appearance as faded by time. Many jobs involve reweaving a damaged area of carpet. Once the appropriate yarns have been chosen and dyed, the warps are fed in (they must not be visible on the front or back), and the section to be worked is stretched over a frame to create a strong tension this is a crucial part of the process. The wefts are then woven horizontally through the warps to create the found-ations on which the pattern will be built. 'Patterns are usually geometric,' says Jill. 'Old handmade carpets have imperfections, and these have to be repeated.' Once the design has been knotted in, the remade section is shaved down to conform with the surface of the original. They also stretch misshapen rugs and treat moth damage, which usually occurs on an undisturbed part?'look for signs of chrysalis, white grubs and the trails they make when munching away'?and give advice on various methods of control. They now travel all over the country, offering advice on the repair and cleaning of carpets and textiles. 'Sometimes we are able to advise an owner that nothing needs to be done.' MARY MIERS Jill Patchett and Alan du Monceau: 01458 253771 TOP TIPS
To preserve a carpet's life, turn it round occasionally, and get a good underlay to help prevent wear on hard surfacesThe sides and ends of carpets tend to be the first areas to deteriorate. Look for signs of loose knots and foundations
Ideally, antique carpets should not be vacuumed. If you must, use only the mildest suction. A gentle carpet sweep is preferable This article first appeared in Country Life magazine on November 9, 2006
For more on property, architecture, the arts and the countryside subscribe to Country Life magazine
Contact us about this story
Search all online stories
For what's in the magazine this week see contents
Sign up for the Country Life Newsletter
Exquisite houses, the beauty of Nature, and how to get the most from your life, straight to your inbox.
Sign up for our free newsletter
Country Life is unlike any other magazine: the only glossy weekly on the newsstand and the only magazine that has been guest-edited by HRH The King not once, but twice. It is a celebration of modern rural life and all its diverse joys and pleasures — that was first published in Queen Victoria's Diamond Jubilee year. Our eclectic mixture of witty and informative content — from the most up-to-date property news and commentary and a coveted glimpse inside some of the UK's best houses and gardens, to gardening, the arts and interior design, written by experts in their field — still cannot be found in print or online, anywhere else.
-
'Monolithic, multi-layered and quite, quite magnificent. This was love at first bite': Tom Parker Bowles on his lifelong love affair with lasagne
An upwardly mobile spaghetti Bolognese, lasagne al forno, with oozing béchamel and layered meaty magnificence, is a bona fide comfort classic, declares Tom Parker Bowles.
By Tom Parker Bowles Published
-
Country houses, cream teas and Baywatch: Country Life Quiz of the Day, April 24, 2025
Thursday's Quiz of the Day asks exactly how popular Baywatch became.
By Toby Keel Published
-
How to prepare your house for winter
As winter approaches, experts advise that preventative measures are crucial for our houses to weather hard winters
By Country Life Published
-
Ten house tips for the winter
Now is the time to put your house in ship-shape for the winter months ahead. Chartered surveyor Tom Grillo shares his ten top tips
By Country Life Published
-
Choosing an interior designer
Finding the right skilled interior designer for your period property requires some dedication; in particular you need to make sure you share the same vision
By Country Life Published
-
Maintenance tips for Victorian houses
There are a number of aspects to look out for when viewing or indeed owning a Victorian house
By Country Life Published
-
Best cooking pans
Mrs Danvers suggests the best makes of pots and cooking pans to hunt down when shopping for a special friend's wedding present
By Country Life Published
-
How to save old floorboards
Lots of care and elbow grease can help old floorboards gleam again
By Country Life Published
-
Buying bellows
Mrs Danvers recommends where to find a new or antique pair of bellows
By Country Life Published
-
Removing chocolate stains
Mrs Danvers tackles readers' household queries: this week's are chocolate stains on a linen suit and screen doors
By Country Life Published